Infrared Thermography
Infrared Thermography technology can detect thermal problems that are undetectable to the human eye. This technology can detect overloaded circuits, faulty or high resistance connections, damaged fuses and clips, and other defective electrical components before they can cause expensive facility damage or production losses. Infrared surveys of electrical switchgear are an integral part of every preventative and predictive maintenance program for facilities management.
Benefits of Having an Infrared Thermography Survey?
- Reduces the risk of electrical fire.
- Reduces the risk of an unplanned electrical outage.
- Identifies priorities for planned maintenance.
- Increases electrical and mechanical equipment service life.
- Reduces downtime.
- Lower maintenance and repair costs.
- Lowers risks from arc flash.
Industry Standard Survey Report Includes:
- Description and location of equipment tested.
- Notation of discrepancies to include electrical code violations or safety hazards.
- List critical equipment not inspected with explanations for the omission.
- Relevant data such as wind speed, direction, precipitation, humidity and ambient air temperature.
- A side-by-side infrared and visible light image of the deficient areas of each piece of equipment (see below for examples)
- Corrective measures for discrepancies and request for follow-up infrared image to document any repairs made.
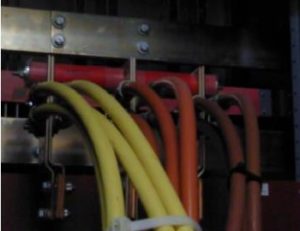
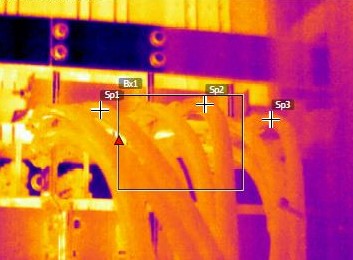
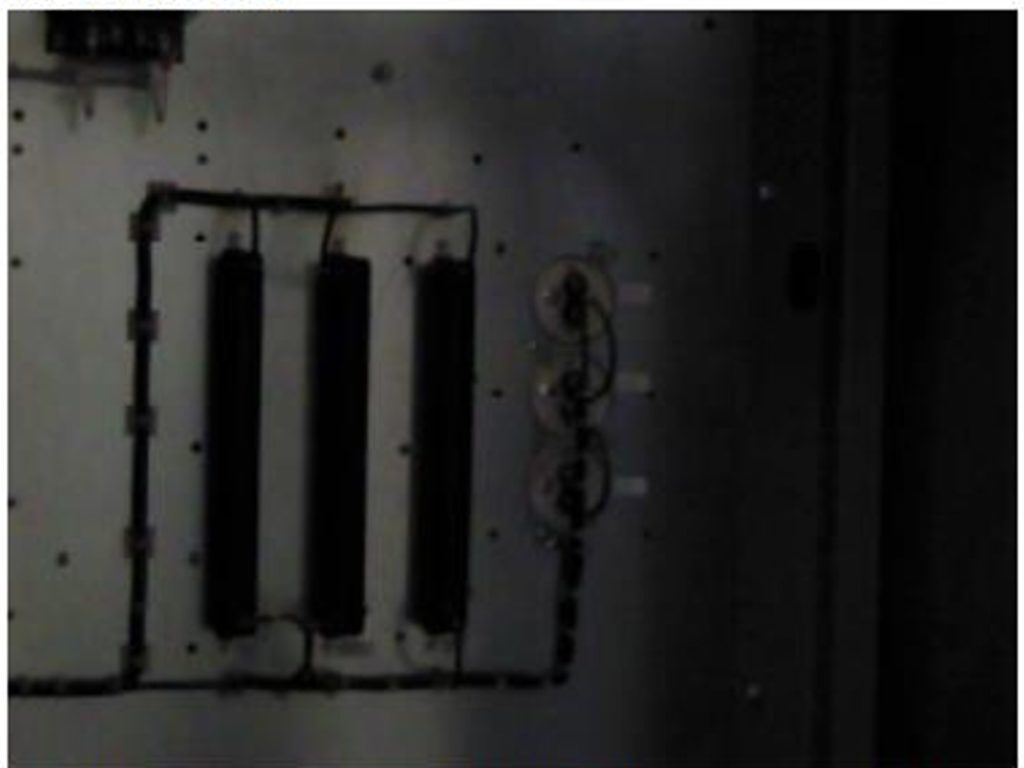
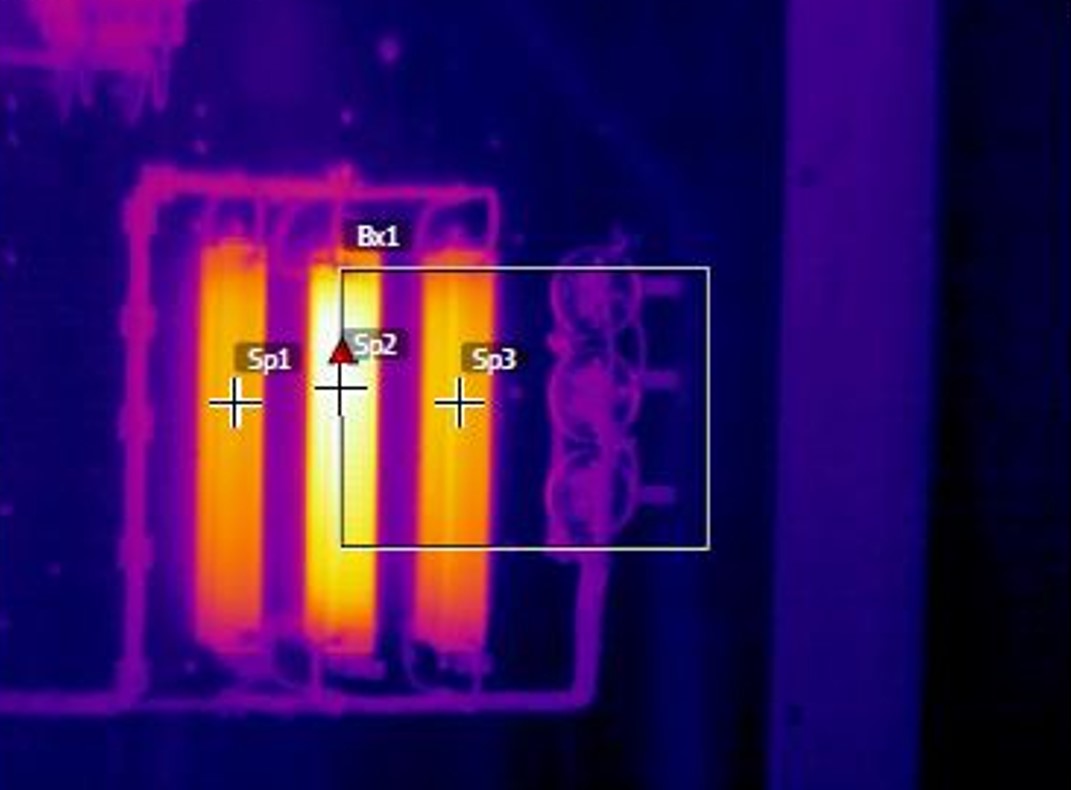
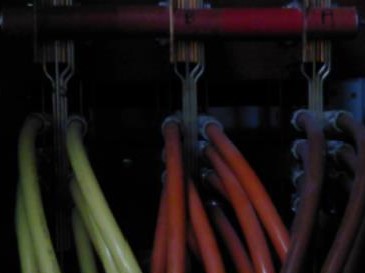
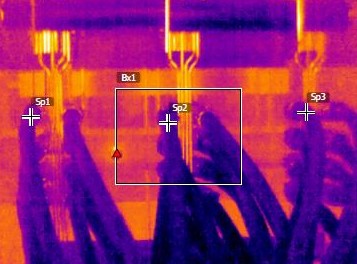